A Coordinated Electric System Interconnection Review—the utility’s deep-dive on technical and cost impacts of your project.
Grid Code Compliance for Wind Farms: A Technical Overview for Electrical Engineers
April 26, 2025 | Blog
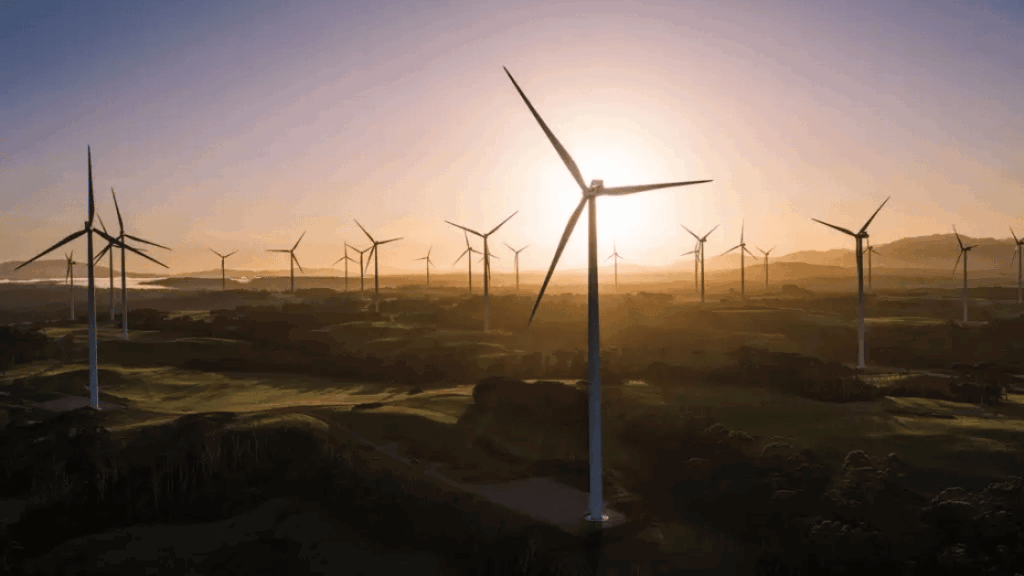
As renewable energy continues to reshape the global power landscape, grid code compliance for wind farms has become a cornerstone of system reliability and performance. At Keentel Engineering, we understand that integrating large-scale wind power into high-voltage transmission systems requires rigorous adherence to international standards.
This article offers a comprehensive technical breakdown of critical interconnection requirements — rooted in decades of global grid code evolution.
Why Grid Codes Matter in Wind Integration
Grid codes are regulatory frameworks established by Transmission System Operators (TSOs) to maintain safety, reliability, and stability across the power system.
For wind farms—especially those connecting at high-voltage levels—compliance ensures their operational behavior mirrors that of conventional synchronous generation during both normal and fault conditions.
Learn more about how electrical substations benefit the grid.
Key Technical Requirements for Wind Farms
1. Fault Ride-Through (FRT) Capability
Wind farms must remain connected during short-term voltage dips.
Global grid codes (Germany, UK, Nordic) require wind plants to withstand dips down to 0% voltage for up to 150 milliseconds.
2. Reactive Power Control and Voltage Regulation
Wind farms must dynamically absorb or supply reactive power to stabilize grid voltage.
Voltage-reactive power curves are mandated in codes like the UK, Germany, and Denmark.
3. Active Power Control and Frequency Regulation
Wind plants must adjust active power based on frequency deviations to support system frequency.
Ireland, Germany, and Hydro-Quebec grid codes require frequency response and curtailment capabilities.
4. Extended Operating Ranges
Wind farms must operate under broader voltage (90–110%) and frequency (46.5–54 Hz) conditions.
5. Data Communication and SCADA Integration
Modern grid codes require real-time SCADA-based communication of voltage, current, power, and operational status.
Technology Behind Compliance: Wind Turbine Types
Constant-Speed Induction Generators
Require external compensation (e.g., capacitor banks or STATCOMs) and struggle with LVRT requirements.
Doubly-Fed Induction Generators (DFIGs)
Offer partial converter control but require crowbar circuits for fault handling.
Full Converter-Based Systems
Provide complete decoupling from the grid, enabling superior voltage control and frequency response.
Global Grid Code Comparison Highlights
Country | Voltage Dip Tolerance | Frequency Range | Reactive Power Capability |
---|---|---|---|
Germany | 0% for 150 ms | 47.5–51.5 Hz | ±0.95 PF |
UK | 0% for 140 ms | 47.5–52 Hz | ±0.95 PF |
Ireland | 15% for 625 ms | 47–52 Hz | ±0.835 PF |
Nordic | 0% for 250 ms | 47–53 Hz | Voltage regulation required |
Canada | 15% for 625 ms | 57–61.7 Hz | Dynamic + continuous PF control |
U.S. Grid Code Requirements for Wind Farms Based on IEEE P2800-2022
Voltage Dip Tolerance (Ride-Through Capability)
Inverter-Based Resources (IBRs) must remain connected and ride through voltage dips based on severity and duration:
- Example 1:
Voltage dip to 60% of nominal voltage for 2.0 seconds → Ride-through is required. - Example 2:
Voltage dip to 60% of nominal voltage for 3.0 seconds → Ride-through is not required.
Minimum ride-through times are detailed in Figures D.1 to D.4 and Section 7.2.2 of IEEE P2800-2022.
The exact requirement varies based on the fault profile and system configuration.
Frequency Range (Ride-Through Capability)
According to Table 15 and Figure 12 in Section 7.3.2.2 of IEEE P2800-2022:
- Continuous Operation Region:
±2% from nominal frequency. - For 60 Hz systems: 58.8 Hz to 61.2 Hz
- Required to maintain full operation indefinitely.
- Mandatory Operation Region:
+3% and −5% from nominal frequency. - For 60 Hz systems: 57.0 Hz to 61.8 Hz
- Required to ride through for at least 299 seconds without tripping.
These thresholds ensure that wind farms contribute to overall grid resilience during abnormal frequency events.
Reactive Power Capability Requirements
Based on Section 5.1 and Figures 6, 7, and Table 4 of IEEE P2800-2022:
- Minimum Reactive Power Capability:
- When injecting active power:
|Qmin| ≥ 0.3287 × ICR (Installed Capacity Rating) - When absorbing active power:
|Qmin| ≥ 0.3287 × ICAR (Installed Capacity Absorption Rating) - Voltage Range for Reactive Power Capability:
- For systems operating at ≥200 kV, the reactive power curve must be maintained across a voltage range of 0.90 p.u. to 1.10 p.u..
- Voltage vs Reactive Power (Q-V) Characteristics:
Plants must continuously maintain Q-V support across all active power operating conditions.
This ensures that wind farms provide dynamic voltage support critical for high-voltage grid stability.
Learn about NERC compliance importance.
Partner with Keentel Engineering for Wind Farm Compliance
At Keentel Engineering, we bring over 30 years of expertise to help you navigate the complexities of wind farm interconnections and grid code compliance.
From collector system design to SCADA integration and dynamic grid modeling, we ensure your project not only meets the technical requirements but thrives in today’s evolving energy markets.
See Our Service: Utility Scale Wind From Engineering
FAQs for Electrical Engineers | Grid Code Compliance for Wind Farms
1. What is Fault Ride-Through (FRT)?
Staying connected to the grid during short-term voltage dips caused by faults.
2. What’s the typical duration for voltage dips in grid codes?
Typically 0.1–0.25 seconds, depending on code and system conditions.
3. How does reactive power help grid stability?
It stabilizes voltage during and after system disturbances.
4. What reactive power range is typically required?
±0.95 power factor minimum; some regions demand ±0.835 PF.
5. What turbine technology best meets grid code requirements?
Full-converter synchronous generator systems.
6. How does pitch control contribute to active power regulation?
Adjusting blade angles to vary output quickly.
7. Why is frequency response important?
To stabilize supply-demand balance and avoid blackouts.
8. Difference between passive and active crowbar systems?
Passive crowbars are less flexible; active systems recover faster after faults.
9. Can constant-speed turbines meet modern grid codes?
Only with external compensation (STATCOMs/SVCs).
10. What is delta production control?
Operating turbines below maximum output to maintain reserves.
11. What role does a DFIG’s grid-side converter play?
Manages reactive power and grid export.
12. What’s the typical recovery time after a fault?
Usually about 1 second to restore 90–100% active power.
13. Why are FRT curves important?
They define required turbine behavior during voltage dips.
14. How is compliance verified?
Through voltage dip tests and simulations (IEC 61400-21 standards).
15. Are offshore wind farms subject to special requirements?
Yes, especially for HVDC integration and data points.
16. What is a “dead band” in voltage control?
A small voltage range where no reactive response is required.
17. What is a stator switch?
Allows turbine disconnection during extreme faults.
18. Are there timed reactive power requirements?
Yes, some codes require reactive injection within 100–150 ms.
19. Can wind farms offer spinning reserves?
Yes, if operated below max capacity for quick ramp-up.
20. Why is SCADA critical for wind farms?
For real-time monitoring, grid interaction, and compliance tracking.
21. What are short-circuit emulator tests?
Simulations of faults to test turbine LVRT capability.
22. How do weak grids affect compliance?
They amplify voltage dips, making FRT and voltage control more critical.
23. Typical ramp rates for active power control?
10–30% per minute; sometimes specified in MW/min.
24. Are reactive requirements consistent worldwide?
No—they vary significantly by country and grid strength.
25. Can one global grid code be applied everywhere?
No, grid codes are highly regionalized based on local grid characteristics.
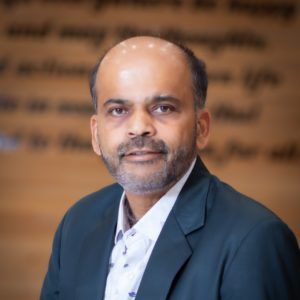
About the Author:
Sonny Patel P.E. EC
IEEE Senior Member
In 1995, Sandip (Sonny) R. Patel earned his Electrical Engineering degree from the University of Illinois, specializing in Electrical Engineering . But degrees don’t build legacies—action does. For three decades, he’s been shaping the future of engineering, not just as a licensed Professional Engineer across multiple states (Florida, California, New York, West Virginia, and Minnesota), but as a doer. A builder. A leader. Not just an engineer. A Licensed Electrical Contractor in Florida with an Unlimited EC license. Not just an executive. The founder and CEO of KEENTEL LLC—where expertise meets execution. Three decades. Multiple states. Endless impact.
Services
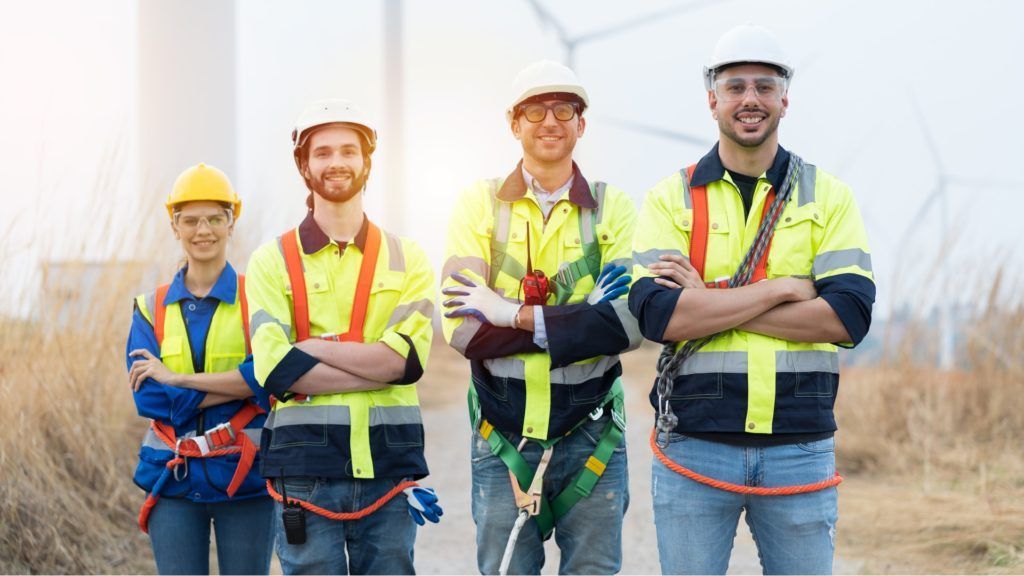
Let's Discuss Your Project
Let's book a call to discuss your electrical engineering project that we can help you with.
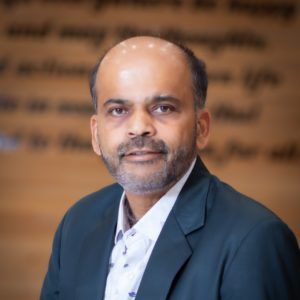
About the Author:
Sonny Patel P.E. EC
IEEE Senior Member
In 1995, Sandip (Sonny) R. Patel earned his Electrical Engineering degree from the University of Illinois, specializing in Electrical Engineering . But degrees don’t build legacies—action does. For three decades, he’s been shaping the future of engineering, not just as a licensed Professional Engineer across multiple states (Florida, California, New York, West Virginia, and Minnesota), but as a doer. A builder. A leader. Not just an engineer. A Licensed Electrical Contractor in Florida with an Unlimited EC license. Not just an executive. The founder and CEO of KEENTEL LLC—where expertise meets execution. Three decades. Multiple states. Endless impact.
Leave a Comment
We will get back to you as soon as possible.
Please try again later.